Публикации
Обоюдная ответственность
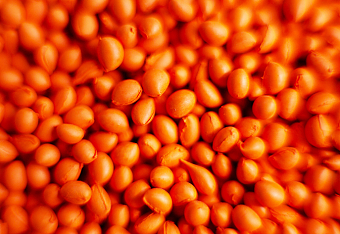
За качество кабельной продукции должны отвечать и кабельщики, и поставщики материалов.
Один из главных элементов системы контроля качества кабельно-проводниковой продукции (КПП) — исследование свойств материалов, из которых делают изоляцию и оболочку кабелей и проводов. Нередко производители меняют состав полимерных композиций, обнаружить изменение рецептуры без серьезных исследований невозможно. Между тем сегодня мало кто из кабельных предприятий может похвастаться наличием технических и технологических возможностей для глубокого анализа поставляемых материалов. «Холдинг Кабельный Альянс» (ХКА) один из первых в отрасли поставил контроль качества полимеров во главу угла. О том, как организован этот процесс на заводах ХКА, рассказал технический директор компании Алексей Саушкин.
— Алексей Викторович, унифицирован ли процесс контроля качества материалов и готовой продукции на предприятиях ХКА или существует специфика в зависимости от видов продукции, производственных цепочек?
— Контроль унифицирован, объем испытаний по каждому виду продукции устанавливается в картах контроля на предприятиях. Другое дело, что проверять после каждого этапа всю продукцию, выпускаемую серийно, нет необходимости, но для новых изделий вводится дополнительный контроль на различных этапах производства.
В нормативно-технической документации на всю выпускаемую продукцию прописаны этапы контроля ее качества, в частности, приемо-сдаточные испытания, которые проводятся непосредственно перед отправкой продукции клиенту, и периодические – раз в полгода-год. Они требуют анализа более широкого диапазона параметров. Кроме того, существует операционный контроль при производстве — на определенных операциях проверяется качество продукции, что позволяет выявить бракованные изделия до приемо-сдаточных испытаний, а значит, избежать всех возможных рисков.
— Расскажите об испытательной базе, в том числе о лаборатории на заводе «Электрокабель».
— На предприятии «Электрокабель» оборудована самая современная лаборатория, где проводится широкий спектр испытаний кабельно-проводниковой продукции. Ежегодно лаборатория пополняется новым оборудованием. Так, в прошлом году приобретен комплекс оборудования для термоанализа, позволяющий осуществлять испытания полимерных материалов на входном контроле — разработаны специальные методики оценки качества материалов через оценку соответствия эталонным образцам. Также данные приборы помогают оценить срок службы будущего изделия, благодаря методу экспресс-оценки.
— Когда уместны экспресс-испытания?
— В том случае, если необходимо в сжатые сроки разработать кабельное изделие, допустим, со сроком службы 60 лет. Традиционные методы оценки занимают в среднем от двух до трех лет, а используя приборы для экспресс-испытаний, можно провести оценку срока службы кабельного изделия в течение нескольких месяцев. Соответственно, это экономит время, и уже на начальном этапе понятно, с какими материалами мы имеем дело.
— Какие требования сегодня предъявляются к материалам?
— В нашем холдинге внедрена система дополнительных требований, что обусловлено, в том числе, существующей проблематикой пожаробезопасности материалов. Дело в том, что поставщики в основном работают по самостоятельно установленным техническим условиям. Мы не согласны с подобным подходом и при заключении договоров устанавливаем свои технические требования, в соответствии с которыми принимаем материалы на процедуре входного контроля.
Кстати, многие кабельные заводы России, озаботившись качеством продукции, выпускаемой из материалов, не соответствующих ГОСТ, также начали предъявлять к поставщикам дополнительные требования. Надеюсь, в ближайшие два года нам удастся навести порядок в данной сфере, и на рынке будут только качественные материалы, ведь от этого напрямую зависит качество продукции.
— Кто должен нести ответственность за поставку, переработку некачественного материала и, как следствие, выпуск некачественного кабеля?
— Речь идет об обоюдной ответственности. В первую очередь, ответственность должны нести поставщики такого материала, но и кабельщики должны занимать более активную позицию: их задача — настроить системы входного контроля, при необходимости приобрести дополнительное оборудование, прописать регламенты проверки. Как только наведем порядок с входным контролем на предприятиях, поставщики некачественных материалов поймут, что теряют рынок.
— Как и чем регламентировано производство кабельной продукции? ГОСТ и ТУ – в чем разница и как разобраться потребителю?
— ГОСТ – это общеотраслевой стандарт, устанавливающий общие требования к кабельному изделию, на основании него производители индивидуально разрабатывают технические условия. При этом в техусловиях должны быть прописаны высокие требования к продукции, ведь при сертификации ее обязательно проверяют на соответствие ГОСТу. В действующей ситуации однозначно сказать, что если Вы покупаете кабель по ТУ, то это кабель плохой – нельзя. Для того, чтобы не ошибиться с выбором, бытовому покупателю лучше ориентироваться на известные компании-производители, которые дорожат своей репутацией на рынке.
— Нужно ли ужесточать требования к такой продукции, чтобы она была безопасной?
— Сегодня стандартами и ГОСТами установлены достаточно жесткие требования, усиливать их нет смысла. В целом, в последнее время наблюдается улучшение ситуации. Большая заслуга в этом проекта «Кабель без опасности», отбирающего образцы кабельной продукции в том числе с объектов массового скопления людей – школ, детских садов, больниц, аэропортов. Применение там некачественной продукции может привести к трагедиям. Периодически встречаемся с коллегами на площадке ассоциации «Электрокабель», обсуждаем проблематику качества материалов, разрабатываем стандарты качества - так называемые технические требования; готовы делиться опытом с единомышленниками.
Беседовала Елена Восканян